Cold-Spray Research Experience
My first experience with professional engineers was on the team of two material science PhDs and leading experts in the cold-spray field. I spent two years studying the process and building fixtures to manipulate the particle stream. In this post I will describe the questions we faced and my solutions.
The Constraints
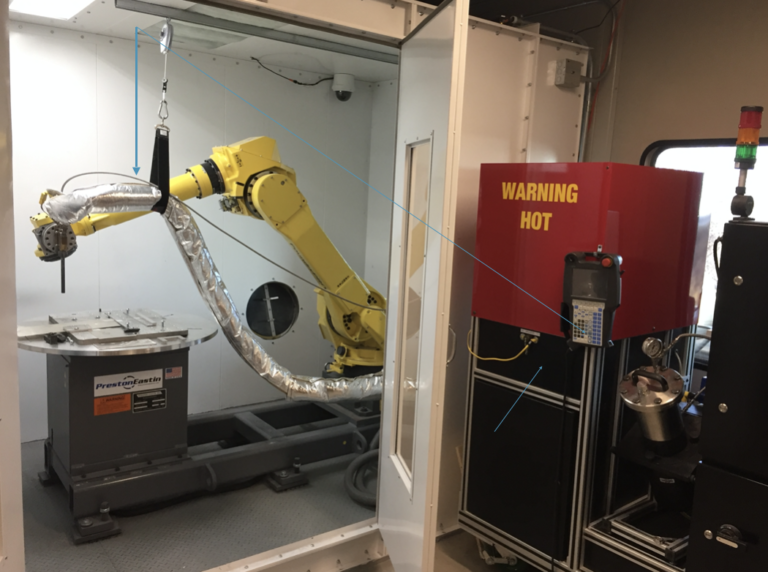
The experiments were begun by programming a 6-axis robot arm to control the nozzle. A metallic powder was sprayed from nozzle at speeds over 1,000 ft/s and temperatures near 800 F which meant that human intervention was permitted during the experiment.
Question #1: How does the spray deposit on rotating objects?
We wanted to see how a surface that was changing orientation and location would receive the cold spray particles. The fixture should demonstrate how cold-spray could be used on a driveshaft or projectile while maintaining convenience of experimentation. We also wanted to see how this would change as more particles bond to the surface and create a top layer. To test this I designed the following fixture that could be attached to a simple motor.
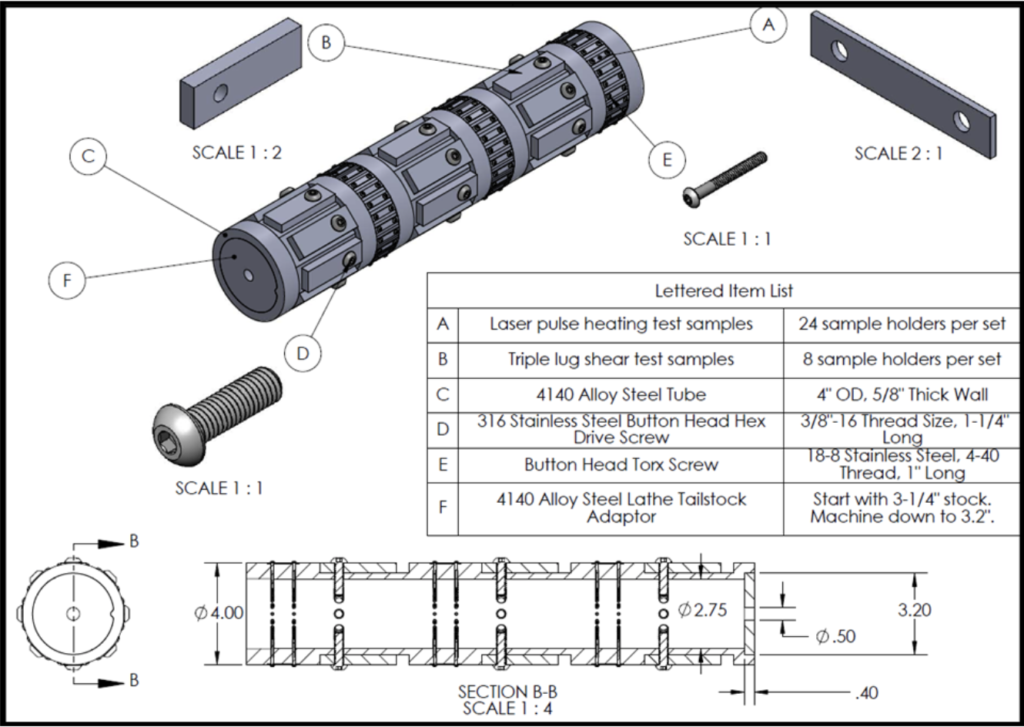
This fixture mimics the shape and movement of a solid shaft but contains over 100 individual samples across six sections that can be tested and analyzed Separately. In the video below an experiment is run using this fixture.
Question #2: What percentage of particles successfully bond to the substrate?
Using this simulation developed in SolidWorks FEM we could estimate how many particles are released in a given time. I then designed a fixture to control the time that the substrate was exposed. The fixture used a slotted disk on a shaft attached to a torsion spring. An drawing of this fixture is attached below.
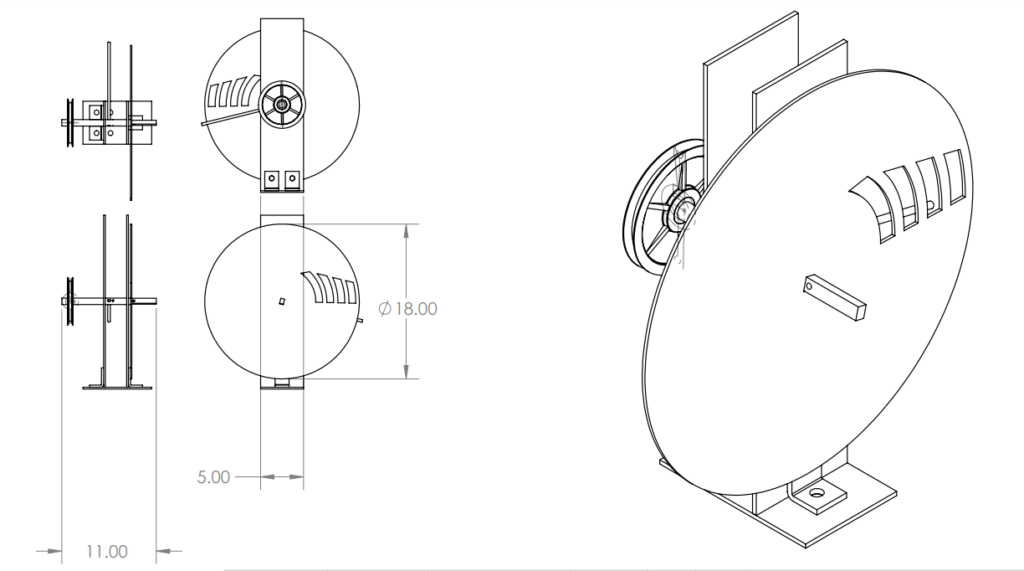