My Experience with MWH Constructors
MWH Constructors is one of the leading general contractors in industrial water & wastewater construction in the US and UK. With them I commissioned a 75 MGD micro-filtration system and a thermal hydrolysis process addition to a 150 MGD plant. I regularly used P&IDs and Manuals to start up autonomous industrial systems built around PLCs and SCADA.
Safety was always a priority on the job sites. I completed the OSHA 10 hour safety course and wrote many job hazard analysis.
Pall Water Micro-filtration Spokane WA
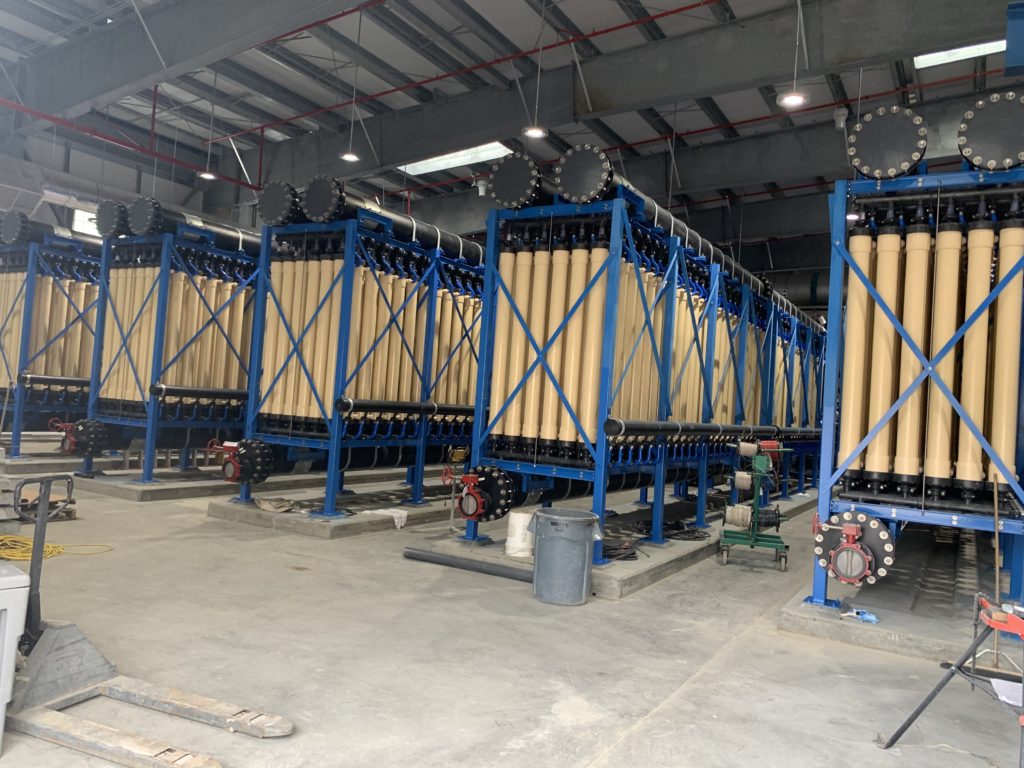
On this project I completed a factory acceptance checklist with the Plant SCADA manager and a field engineer from Pall Water. Over four months we signed off over 5000 items in the categories functionality, graphics, and alarms. During this commissioning I was the sole representative of the general contractor, giving me the responsibility of coordinating repairs when problems arose. Examples are included later in this post.
THP Solids Handling Upgrade Dallas TX
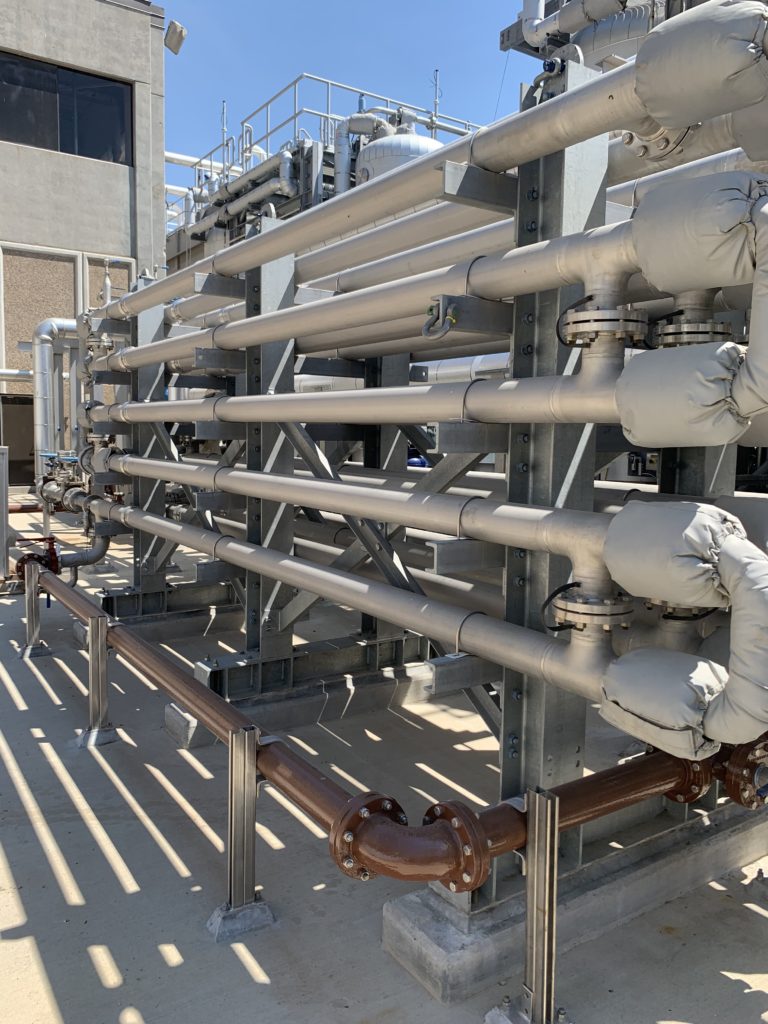
In Texas on worked on a team commissioning gravity belts, centrifuges, boilers, and many other pieces of equipment used in wastewater solids handling. during my two months on this site our main goal was to complete site acceptance tests (SATs) for the five gravity belts we had just constructed. I worked with the CDM smith design engineer and the plant inspectors to run the gravity belts for seven days without interruption. This involved overseeing operators and troubleshooting the gravity belts when problems arose.
Leaky Diaphragm Pumps
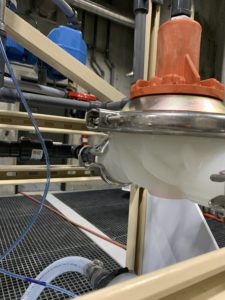
I discovered leaks on diaphragm pumps that provided chemicals to larger chemical batch tanks. There were leaks in multiple locations. The first thing I did was secure the area with “danger” tape because citric acid was one of the chemicals leaking. I then contacted a pipe-fitter to examine the pumps and tighten any loose connections. When there was still leaking I talked to my manager and we ordered a rebuild kit from the pump manufacturer. Using proper PPE and a technical manual I worked with the pipe fitter again to install the rebuild kits. This fixed the leaks.
Swapped Chemical Lines
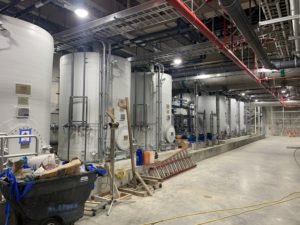
One of these chemical tanks was not filling up when we turned on the feeding pump and opened the necessary valves. I first checked that the pump was running and the valves were open. Then I checked the level transmitter on the tank to see if it was really not filling. After this I traced the line from the pump to the tank and found that a different tank was being filled. I corrected this by swapping the air lines on two pneumatic valves near the outlet of the pump.
Tanks Overflowing Foam
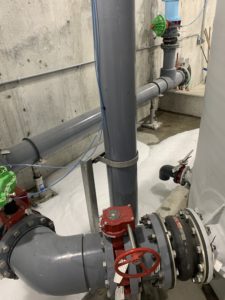
When testing a cleaning sequence I smelled a strong chlorine scent and found chlorine foam. The foam was contained in a basin so the area was easy to contain with “caution” tape. I spent the next month collecting data on the situation. This included which tank, time of day, time since last clean, what was being cleaned, and how much foam was created. I worked with my manager to submit an RFI on the topic and many theories were fleshed out. With this data we learned that if the filters were cleaned at least once per week they would not create foam. This was within the expectations for the system.
Alarm Latching
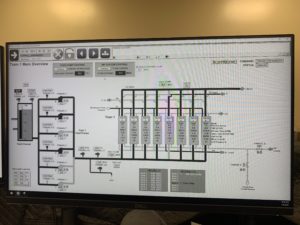
Of all the problems we encountered in SCADA the alarm latching ws the most significant. After an alarm was triggered and the alarm state was removed, the alarm would not stay latched and would fully clear as if the alarm had never happened. I worked with the vendors programmers to fix this issue for hundreds of alarms over the course of a few weeks.
Summary
I had the opportunity to get hands on experience with the hardware that is used by many automated industrial systems. I learned that I enjoy being on site working with tangible problems.